Trimet takes the next step to CO2-free aluminium product
by David Fleschen
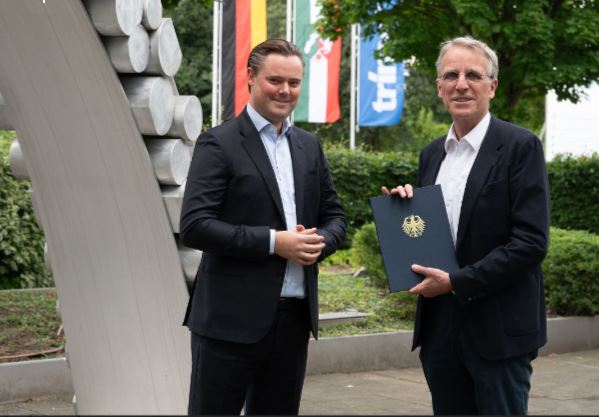
Aluminium producer Trimet is pressing ahead with the development of a new technology for the CO2-free production of aluminium. The materials specialist is commissioning a demonstrator plant at its production plant in Essen to test the technology on an industrial scale. The project is being funded by the German Federal Ministry for Economic Affairs and Climate Protection with around three million euros as part of the "Decarbonisation in Industry" funding programme. Funds from the European Union's "NextGenerationEU" fund are also being utilised. On 8 July, Stefan Wenzel, Parliamentary State Secretary to the Federal Minister for Economic Affairs and Climate Protection, handed over the funding decision and visited the aluminium smelter to find out about the production of the light metal and the progress of the project.
"Transformation remains a challenge for the industry," says State Secretary Wenzel. "I am delighted that Trimet is leading the way and developing technologies that will help us move towards climate neutrality while maintaining value creation and jobs in Germany."
Together with partners from research and materials development, Trimet has developed an innovative process that does not release any carbon dioxide during aluminium electrolysis and therefore reduces direct CO2 emissions during metal production to almost zero. Following the successful completion of the pilot phase, Trimet will now test the technology in three electrolysis furnaces under production conditions.
"The green transformation needs aluminium. This makes it all the more important to produce this material in such a way that vehicles, energy systems, packaging and the other products in which it is used benefit from its ecological quality," says Philipp Schlüter, CEO of Trimet Aluminium SE. "By developing emission-free furnace technology and making the production process more flexible, we are gearing our aluminium smelters towards the goal of climate-neutral aluminium production."
Aluminium is produced using fused-salt electrolysis. In this chemical process, electricity is fed into the starting material, aluminium oxide. The anodes and cathodes required for this consist of carbon, which is consumed during production and releases CO2 in the process. The process developed by Trimet uses so-called inert anodes and cathodes. They consist of a material that releases oxygen instead of carbon dioxide during the electrolysis process, thus avoiding the emission of greenhouse gases that are harmful to the climate.
In energy-intensive aluminium production, it is primarily the CO2 emissions from electricity generation that affect the material's carbon footprint. The increasing share of renewable energies will significantly reduce the CO2 footprint of aluminium. In recent years, Trimet has converted its production sites so that they can flexibly process fluctuating amounts of electricity from wind power and photovoltaic systems. With inert furnace technology, the family-owned company is preparing to produce aluminium in a climate-neutral way.
Source and Photo: Trimet