Predicting the Future
by Hans Diederichs
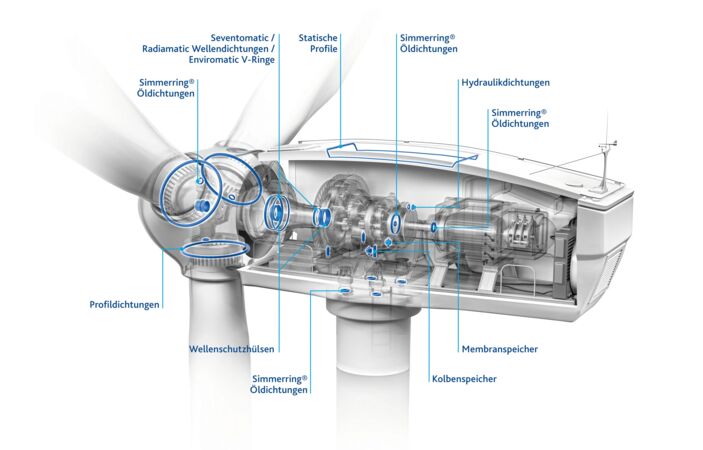
Freudenberg Sealing Technologies has developed an advanced testing procedure and simulation methodology that, in combination with the company’s Ventoguard portfolio of elastomeric materials, offers performance improvements and better longevity in offshore wind energy component applications. The material simulation process helps to identify optimal materials and designs for wind applications by analysing how materials behave and function over the lifetime of a turbine. Recently, the process has been used to identify the best materials and designs available to protect turbine foundations from moisture and deterioration.
Growing demand for power derived from clean energy sources is driving installation of new offshore wind turbines throughout the world. The wind is an economically inexpensive and abundant resource to harvest, and offshore wind turbines are expected to reach a total installed power of 1,000 GW, enabling wind power to supply 35 percent of the world’s total energy demand by 2050. As more turbines are pressed into service, however, new challenges are emerging for commercial operators and manufacturers. Wind farms are being located farther offshore in deeper waters, turbines are becoming larger to generate more power and maintenance of these gigantic systems is becoming more costly and challenging.
“Two predominant trends to emerge in the industry are an increase in the size of the offshore wind turbines and their location farther offshore,” said Marcel Schreiner, Global Segment Director, Energy, Freudenberg Sealing Technologies. “These trends are putting pressure on engineers to design offshore systems that can handle harsh environmental conditions, maintain structural stability and offer long-term functionality and lifecycle use with minimal maintenance requirements. Freudenberg has focused its expertise on meeting these expectations and requirements.”
Continuous research, development and testing
The lifetime of the average wind turbine is more than 26 years – which can push standard materials and components beyond their ability to function. For example, in Monopile construction, the Monopile Transition Piece (MP/TP) flange seal and the inlet for high voltage cables must be impervious against moisture and corrosion well beyond two decades. Efforts to predict the performance capabilities of turbine seals and components requires continuous research, development and testing.
In response, experts at Freudenberg have developed a new testing process that can accurately assess how long and how well a material will perform in aggressive offshore wind environments. By determining a material’s relaxation rates at different temperatures, Freudenberg specialists are able to convert the acquired information into a mathematical curve which can be used for Arrhenius extrapolation. The method then helps to simulate aging in elastomeric materials, allowing engineers to predict the lifetime of seal components. By comparing new profiles with those aged the equivalent of 26 years under harsh offshore wind turbine conditions, Freudenberg has been able to create more robust sealing solutions for the MP/TP flange seal and high voltage cable inlet seals, among others.
The Ventoguard family
The company has also developed a family of unique materials under its Ventoguard label that offer greater longevity and better performance in wind turbine components. The Ventoguard portfolio encompasses material solutions for a wide range of offshore wind applications. Ventoguard seals are made of nitrile butadiene rubber (NBR), a high-performance synthetic rubber that not only exhibits high resistance to grease, oils and hydrocarbons but is also insensitive to temperature fluctuations, water, salt, grout and ozone. NBR also exhibits a favourable aging behavior and low abrasive wear. These materials perform better than other commercial alternatives, when used in combination with a sophisticated single or dual seal design. The resulting seals are extremely robust, prevents ingress of salt water, thereby preventing foundation damage.
Other wind turbine components from Freudenberg, including globally-certified seals and pressure accumulators, also help these gigantic energy systems to operate efficiently and minimize unplanned maintenance by reducing pre-charge losses and accommodating pressures of up to 350 Bar or 5,000 psi.
Source and graphic: Freudenberg Sealing Technologies