New orders for SMS group
by Hans Diederichs
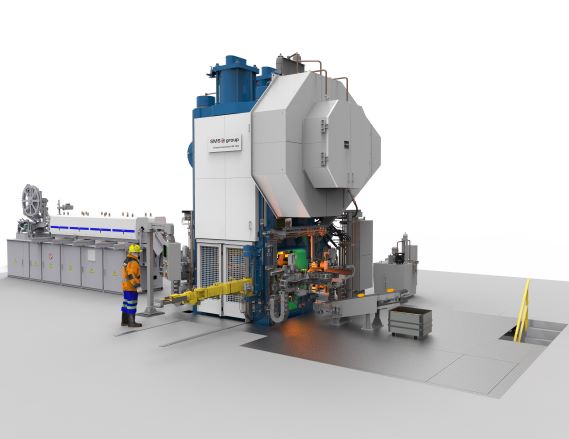
SMS group received new orders from China and the US
Anhui Anhuang Machinery orders fully automatic piston forging line
Anhui Anhuang Machinery Co., Ltd., based in Anqing in the Chinese province of Anhui, has placed an order with SMS group for a fully automatic closed-die forging line for pistons. Anhui Anhuang will be one of the first automotive suppliers in the field of massive forming in China that is capable of manufacturing pistons for cars and trucks in a fully automated process. For SMS, this is the first reference customer in China for a closed-die forging line for pistons. The 2,500-t forging line to be delivered consists of a fully automatic eccentric closed-die forging press of type MP 2500 and an ELO-FORGE L induction heating system from SMS Elotherm, an SMS company, for heating the forging blanks.
The cost efficiency of the whole process is significantly improved as the forging line is fully automated. Car pistons can be forged in a cycle time of less than four seconds. The flashless precision forging process also saves material and energy costs during production: only the exact amount of material required to forge a piston without cutting scrap is heated and used. Other machining steps can be reduced thanks to the high dimensional accuracy of the forged parts. An integrated process control system permanently monitors the entire line and, if necessary, is able to evaluate the production data saved.
The induction heating system from SMS Elotherm has a capacity of 800 kW that enables the forging blanks to be heated to a temperature of 1,220°C. With a throughput of around 2 tons per hour and a cycle time of 2.2 seconds, the modular heating system works in perfect harmony with the SMS forging line. Energy-efficient production is possible in any operational state thanks to a consistently high cos phi power factor. This results in energy savings of up to 30 percent under production conditions. The material feed system and the fully automatic discharge unit are an integral part of the plant concept and enable forging right up to the last part under production conditions within the specified cycle.
The 25-MN closed-die forging press is equipped with an automatic walking beam, a die spraying unit, and a die holder with quick-change system. Important features of the forging press are the electrohydraulic clutch-brake system and the programmable single ejectors for each forging operation.
The use of an electrohydraulic clutch-brake system, which is fitted with a wet multiplate clutch, means that no wear-related readjustments are required. Not only that, but no compressed air is also required to operate the brake and clutch. Other advantages include the high repeat accuracy of the switching operations and associated with this, extremely low noise levels.
The automatic walking beam developed by SMS has a separate servo drive with series-connected gear unit for each axis. The servo drive ensures a smooth and finely-tuned sequence of movements.
The spraying manipulator developed by SMS is mounted on the rear side of the press, providing clear access to the die space. The spraying and drying times for each individual forging operation can be programmed individually.
Ames orders secondary copper smelter
SMS group is supplying a secondary copper smelter to Ames Copper Group, a joint venture between Prime Materials Recovery Inc. and Cunext Group, for the facilities in North Carolina, U.S.A.
The plant will produce up to 50,000 tons of copper anodes annually. The plant start-up is scheduled for 2021.
The new plant will be the first secondary copper recycling facility in the United States to produce copper anodes from copper scrap and copper fines.
SMS scope of supply will include a tilting refining furnace, anode casting wheel, gas cleaning system, and electric and automation systems. In addition to the equipment supply, SMS will provide technical assistance for the installation and start-up and be responsible for the layout of the core equipment. The plant will be prepared for a future upgrade with additional digitalization features.
Source and photos: SMS group
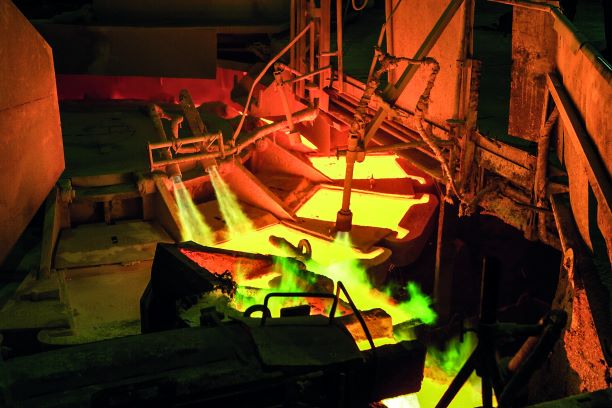