How driverless shuttles get safely from A to B
by Hans Diederichs
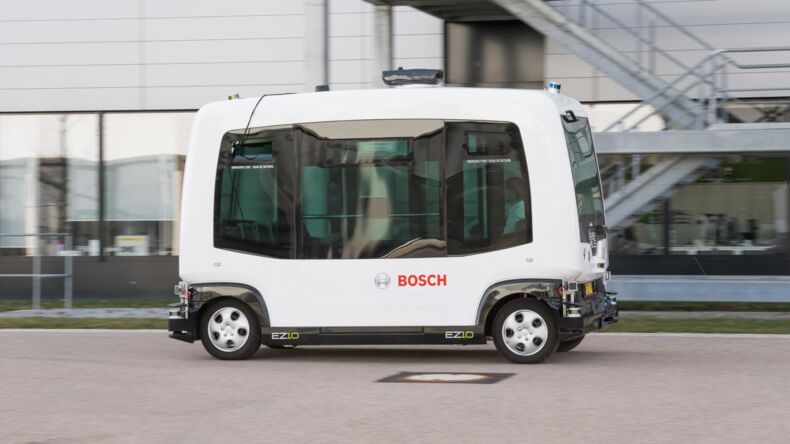
Ferrying visitors from tram stop to exhibition center, supplementing public transport routes, moving containers full of packages in a logistics center: all these are possible use cases for driverless shuttles. The main thing is for them to be able to get safely from A to B – safely in both senses: reliably and without danger. This is what Project 3F, “Driverless and fault-tolerant vehicles in the low-speed range,” set out to achieve, with a focus on fail-safe operation. “The aim was to develop solutions to ensure that automated shuttles can move around safely, even if a technical malfunction occurs or obstacles suddenly appear,” says Steffen Knoop, project leader in research and advance engineering at Robert Bosch GmbH.
Specifically, the project team was concerned with making sure that the system does not fail completely in the event of a fault, but rather that the vehicle can continue to drive. With 4.3 million euros in funding from the German Federal Ministry of Economic Affairs, the project featured Bosch as the consortium leader and involved three other companies, a university, and a research institute: StreetScooter GmbH, RA Consulting GmbH, the FZI Research Center for Information Technology, Finepower GmbH, and RWTH Aachen University.
Better safe than sorry: redundant power supply and sensor technology
“Driverless shuttle buses need to meet different requirements than, say, highly automated passenger cars,” explains Bosch project coordinator Thomas Schamm. To operate without (safety) drivers, shuttles must be able to monitor their system autonomously – in other words, perform diagnostic tasks – and cope with any technical faults detected so that they can continue driving. At the same time, they must be able to secure the system in the event of critical faults, for example by bringing themselves to a stop. Project 3F has been working on what the requirements look like in detail, how the systems must be designed on that basis, and how to optimize the way the individual components interact.
One solution is to build in redundancy, in other words to duplicate safety-relevant functions. For example, the researchers developed redundant systems for the power supply so that the electrical powertrain and vehicle electrical system are reliably protected. They also adapted and refined the sensor technology to suit the vehicle design. In order to reliably detect obstacles, they installed several lidar and radar sensors at various points around the vehicle, giving it the ability to observe its surroundings from different positions. By delivering a 360-degree birds-eye view and avoiding blind spots, this creates a kind of 3D protection zone. This setup not only detects obstacles on the road, such as barriers, it also spots things like hanging branches.
Detect, classify, adjust driving behavior
Another solution is to build in fault tolerance, whereby the failure of a subsystem is at least partly compensated for by other functions. This is a bit like how it is with people: if the lights suddenly go out in a room, we use our other senses and feel our way around instead of becoming paralyzed. The shuttle behaves in a similar way: if it is blind in a certain area, say because leaves are stuck to the sensor or a large object such as a dumpster is completely blocking the view in one direction, it slows down or omits the parts of the route that can no longer be detected.
In addition, the project worked to ensure that shuttle buses can also react to altered circumstances along their defined route. The vehicles are programmed to slow down when any moving objects approach or, in case of doubt, to give unknown objects a wide berth. When they identify familiar landmarks such as streetlights, on the other hand, they resume their journey at full speed. If there is any imminent danger, the shuttle will come to a precautionary stop. The objective is for the vehicle to adapt its driving behavior to the circumstances in real time while also continuing on its journey automatically whenever possible, even in the event of system malfunctions or obstacles in its path.
Three times the telemetry, twice the usability
Data on the journey being undertaken and the current technical status can be transmitted from the vehicle and back to it. Information on three different functions is transmitted back and forth: diagnostics, monitoring, and control. So that is three times the telemetry, which is why we’re calling it “teletrimetry.” This lays the foundation for an entire fleet of automated shuttle buses to be remotely monitored, as well as repaired or even controlled, for instance to open the doors. It means the vehicles will get help if they do ever reach their fault-detection and compensation limits, or if they simply require scheduled maintenance.
The solutions developed in the project work not only for driverless shuttle buses. They can also provide robust support for logistics processes. Project members developed an assistance system for driver-vehicle interaction that enables highly accurate positioning of swap body lifting trucks – special vehicles for moving containers in logistics centers. The objective here was to move the vehicles with centimetre precision underneath gantry cranes to enable the swift removal of transport containers. This requires precise localization and a form of automated parking under the gantry. In practice, this automated maneuver enables error-free container collection and positioning.
These developments were tested on several test tracks: at Bosch’s research campus in Renningen, two shuttle buses tested the transportation of people around a site shared with pedestrians; while at an innovation park near Aachen and in the area around a Deutsche Post/DHL depot, a logistics vehicle was deployed to test the interaction between driver and automated vehicle.
Source and photo: Robert Bosch GmbH